Combinatorial optimization is transforming facade engineering by minimizing material waste during panel production. By applying advanced algorithms, facade engineers and architects can efficiently unfold and nest panels, reducing fabrication waste by up to 11%. This approach balances design intent with material efficiency, enabling sustainable and cost-effective solutions. Metaheuristic algorithms and 2D cutting stock methods further enhance material utilization. Combined with automation and real-time quality control, these innovations empower professionals to create high-performance facades that align with sustainability goals while maintaining aesthetic and structural integrity.
Cutting Waste, Not Corners
The Role of Combinatorial Optimization in Facades
Combinatorial optimization in facade panel design is a sophisticated approach to finding the most efficient arrangement of panels, aiming to minimize material waste during production. The key principles involve efficient panel unfolding to maximize material usage, optimal nesting of cut patterns to reduce scrap, and striking a balance between design intent and material efficiency. These principles are applied to complex facade geometries, enabling architects and engineers to create sustainable designs while simultaneously reducing costs.
The relevance of this approach to sustainable construction is significant. Optimized panel production can lead to a reduction in material waste by up to 11%, substantially lowering the environmental impact of facade manufacturing. This not only contributes to more sustainable building practices but also aligns with the growing industry focus on resource efficiency and waste reduction 1.
Novel Algorithms for Panel Optimization
Unfolding algorithms explore two main approaches:
- Enumerative: Systematically evaluates all possible unfolding options
- Metaheuristic: Uses intelligent search strategies to find near-optimal solutions quickly
For large-scale projects, metaheuristic approaches are often favored due to their efficiency in handling complex geometries 1.
The 2D cutting stock algorithm for optimal nesting configurations uses metaheuristics to determine the best layout of cut panels on raw material sheets. This algorithm considers factors such as panel shape, size, and quantity to maximize material utilization and minimize waste 1.
These advanced algorithms enable facade engineers to create more sustainable and cost-effective designs by optimizing material use in production.
(1) https://ascelibrary.org/doi/abs/10.1061/(ASCE)CO.1943-7862.0002089
The Automation Advantage
How Technology is Revolutionizing Facade Production
File-to-factory systems and automation have revolutionized facade panel production, significantly enhancing efficiency and precision, and enabling intricate designs and consistency across large production runs.
Beside that, quality control in production has become increasingly sophisticated, with computerized inspection systems integrated directly into production lines. These systems can detect flaws and ensure each panel meets rigorous standards, maintaining a balance between mass production and high product quality. For glass facades, quality control involves multiple stages, including checks before construction begins, upon material arrival, during construction, and at project completion.
Real-World Applications: Achieving Waste Reduction Through Optimization
A comparative analysis of different optimization strategies reveals the significant impact of advanced manufacturing techniques on waste reduction. One approach involves using genetic algorithms for multi-objective optimization, such as the Non-dominated Sorting Genetic Algorithm (NSGA-II) 2. This method allows designers to balance multiple performance criteria, including material efficiency, while optimizing panel geometry.
Another strategy employs parametric modeling combined with daylight simulation tools to optimize facade panel configurations. In one study, researchers used Rhinoceros 3D, Grasshopper, Climate Studio, and Octopus software to analyze and optimize panel angles for both daylight performance and material efficiency 3.
Quality control in the production of optimized panels has been significantly enhanced through the integration of real-time monitoring systems. Laser scanning and computer vision technologies are employed to verify panel dimensions and surface quality against digital models. Advanced metrology equipment ensures that each panel meets stringent tolerances, crucial for the proper assembly of complex facade systems.
Furthermore, data analytics and machine learning algorithms are being implemented to predict and prevent production issues, continuously improving the manufacturing process and reducing waste. This proactive approach to quality control ensures that the benefits of panel optimization are fully realized in the final product.
Challenges and Future Developments
Scaling optimization for large-scale projects presents a significant challenge. As facade complexity increases, so does the computational power required for optimization algorithms. Developing more efficient algorithms and leveraging cloud computing are potential solutions to address this issue.
(2) https://research.tudelft.nl/files/177311073/1-s2.0-S036013232400026X-main-1.pdf
(3) https://dergipark.org.tr/en/download/article-file/2140871
Case study
Rigshospitalet, Copenhagen, Denmark (2021)
Architects: LINK Arkitektur and 3XN in collaboration with Nickl & Partner
Client: Region Hovedstaden (Capital Region of Denmark)
The North Wing extension at Rigshospitalet in Copenhagen, designed by LINK Arkitektur and 3XN, exemplifies advanced facade engineering integrated with computational optimization. The 25,000 m² facade employs prefabricated HansenUnitAl panels with natural stone cladding and integrated sun shading. Combinatorial optimization techniques, particularly genetic algorithms (GA), were likely utilized to balance variables such as window-to-wall ratios, U-values, and shading systems. These heuristic methods enabled efficient exploration of design permutations, accommodating complex objectives like daylight maximization, energy efficiency, and urban integration. The facade’s modular design reflects multi-objective optimization principles, addressing noise reduction, daylight penetration, and logistical efficiency. Computational workflows integrated with 3D CAD tools streamlined simulations, ensuring solutions met clinical and environmental targets. The result is a dynamic, V-shaped structure that harmonizes with Copenhagen’s urban fabric, enhancing spatial navigation and patient well-being.
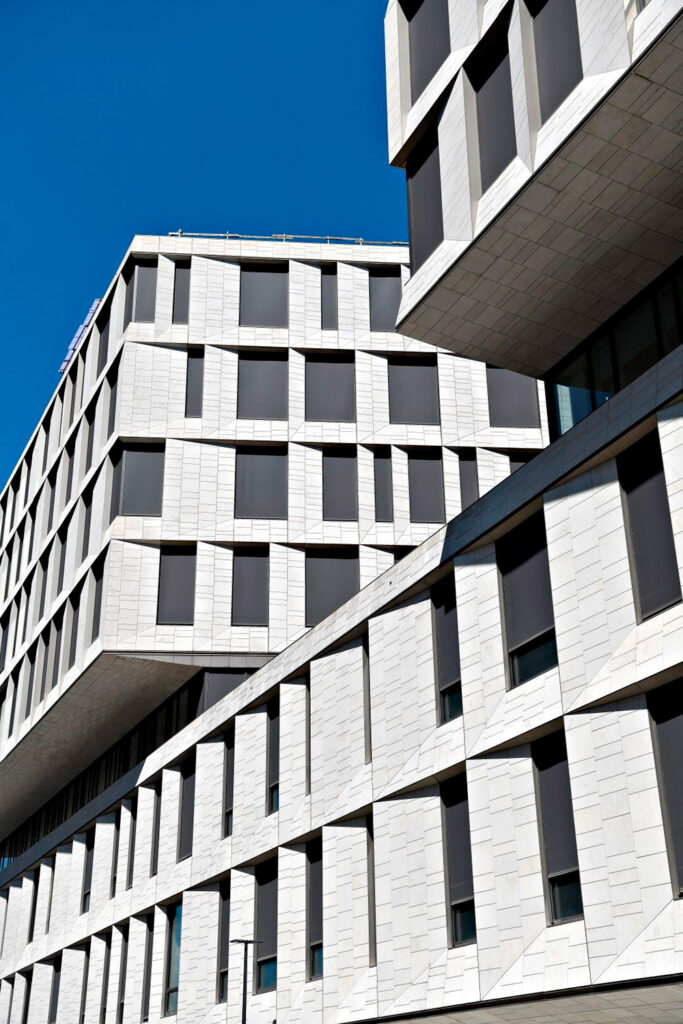