Facade engineers and architects are leveraging Fiber-Reinforced Polymer (FRP) panels to revolutionize building envelopes. These lightweight, durable materials offer superior strength, corrosion resistance, and thermal insulation. FRP’s design flexibility allows for complex geometries and custom textures. Advanced manufacturing techniques, including automated processes and real-time monitoring, ensure precision and quality. The integration of digital design tools and potential for embedded sensors promise a future of smart, adaptive facade systems.
The Silent Performer
Where Strength Meets Lightness
Fiber-Reinforced Polymer (FRP) panels are composite materials made from high-strength fibers, such as glass or carbon, embedded in a polymer matrix like epoxy or polyester. This combination results in lightweight yet highly durable panels with excellent tensile strength, corrosion resistance, and thermal insulation properties. FRP panels are non-conductive, making them ideal for applications requiring electrical insulation, and their low thermal conductivity enhances energy efficiency in building facades.
Compared to steel, aluminum, or wood, FRP panels offer superior corrosion resistance, ensuring long-term durability with minimal maintenance. They are significantly lighter than metals, reducing transportation and installation costs while maintaining comparable strength-to-weight ratios. Additionally, FRP allows for greater design flexibility, enabling the creation of complex geometries and custom textures tailored to architectural needs. These advantages make FRP an increasingly popular choice for high-performance facade systems.
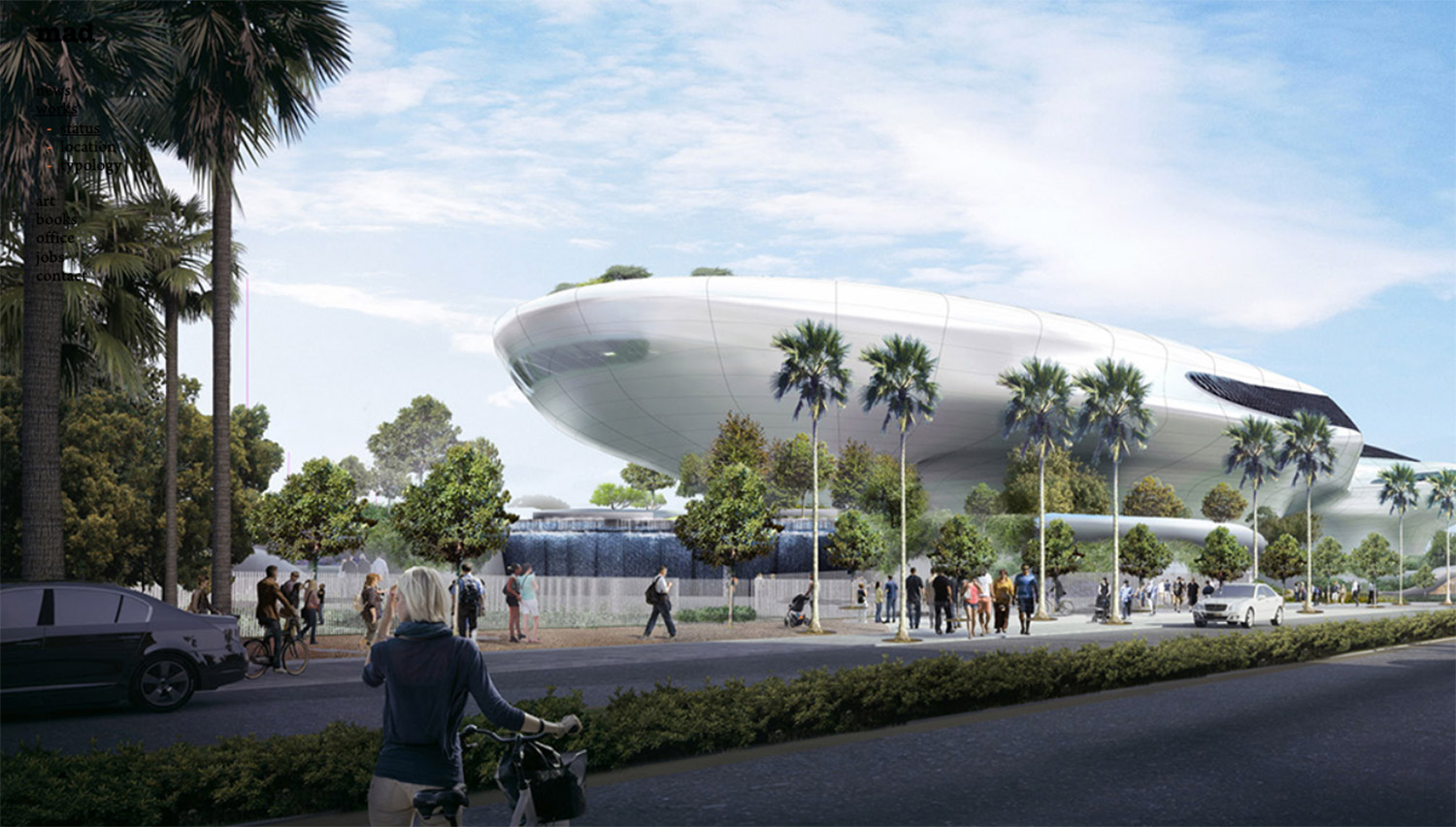
Design Freedom
The Limitless Palette of FRP Facades
Fiber-Reinforced Polymer (FRP) facade panels offer architects unprecedented design flexibility, enabling the creation of visually striking and highly customized building envelopes.
Customization options for architects FRP panels can be molded into virtually any shape, color, or texture, allowing architects to realize their most ambitious design concepts. The material can mimic natural materials like stone or wood, or create entirely new visual effects. Color options are virtually limitless, with the ability to incorporate custom pigments directly into the resin matrix.
Creating complex geometries and textures The moldable nature of FRP enables the fabrication of complex, three-dimensional geometries that would be challenging or impossible with traditional materials. Architects can design intricate patterns, undulating surfaces, or large-scale sculptural elements. Textured finishes can be easily integrated during the manufacturing process, ranging from subtle embossing to dramatic relief patterns. This versatility allows for the creation of unique, eye-catching facades that can define a building’s identity and enhance its interaction with its surroundings.
Precision in Every Layer
Digital Design, Advanced Manufacturing, and Embedded Intelligence
The production of Fiber-Reinforced Polymer (FRP) facade panels has been revolutionized by automated manufacturing processes. Computer-controlled machines now handle the precise layering of fibers and resin, ensuring consistent quality and reducing human error. Robotic arms equipped with spray nozzles apply resin evenly, while automated cutting systems shape panels with remarkable accuracy. These processes not only increase production efficiency but also allow for greater complexity in panel designs.
FRP Done Right: Certifications, Compliance & On-Site Expertise
Quality control in FRP panel fabrication has been significantly enhanced through the integration of real-time monitoring systems. Sensors embedded in production lines continuously assess factors such as resin viscosity, fiber orientation, and curing temperatures. This data is instantly analyzed, allowing for immediate adjustments to maintain optimal production parameters. Non-destructive testing methods, such as ultrasonic scanning and thermography, are routinely employed to detect any internal defects or inconsistencies in the finished panels.
The integration of digital design tools with manufacturing processes has opened new possibilities for customization and performance optimization. Building Information Modeling (BIM) software now directly interfaces with production systems, allowing architects and engineers to fine-tune panel designs based on real-time manufacturing feedback. This seamless digital workflow enables rapid prototyping and iterative design improvements.
A reputable FRP manufacturer will have in-depth expertise in regulatory requirements and be able to demonstrate full compliance with industry standards such as the OSHA or GREENGUARD requirements. Certifications such as ISO 9001, FRPI SP9000 Laminating Process Certification, or other quality management systems are key indicators of a manufacturer’s ability to meet stringent project specifications while ensuring durability, safety, and performance.
While many FRP components are prefabricated for seamless installation, certain applications—such as structural reinforcements and specialized infrastructure—require on-site adjustments and expertise beyond the scope of general contractors. Choosing a manufacturer that offers on-site support, including installation guidance, maintenance, modifications, and inspections, ensures long-term reliability and compliance with project requirements.
Furthermore, the potential for embedding sensors and connectivity within FRP panels during fabrication is being actively explored. These “smart” panels could provide real-time data on structural integrity, thermal performance, and environmental conditions. Such capabilities would enable proactive maintenance and performance optimization throughout the building’s lifecycle. As these technologies mature, we can anticipate a new era of responsive, data-driven facade systems that continuously adapt to changing environmental and occupant needs. In conclusion, FRP panels are revolutionizing facade engineering with their unique combination of strength, lightness, and design flexibility. Advanced manufacturing techniques and digital integration are pushing the boundaries of what’s possible in building envelopes. As the technology matures, we can expect FRP facades to play a crucial role in creating smart, adaptive, and sustainable buildings of the future.
Case study:
Lucas Museum, Mos Angeles (2024)
Architects : MAD Architects
Photography: Virgile Simon Bertrand MAD Architects‘ Lucas Museum of Narrative Art in Los Angeles showcases innovative use of fiber-reinforced polymer (FRP) in facade design. The museum’s striking organic form is achieved through over 1,500 uniquely shaped FRP panels, each measuring approximately 8 by 32 feet. This material choice enables the creation of the building’s fluid, cloudlike exterior while keeping the structure lightweight enough for its base isolation system to function during earthquakes. The FRP panels are fabricated using cutting-edge digital technology and robotics, combined with handcrafting for smoothness and color consistency. This approach allows for complex geometries that would be challenging with traditional materials. The museum, set to open in 2025, will feature 100,000 square feet of gallery space, two theaters, and extensive gardens designed by Studio-MLA. The project demonstrates how advanced materials and manufacturing techniques can push the boundaries of architectural design and performance.